Maintenance planning... magic or mess?
Many mines have high expectations from maintenance planning, but very often the delivery is not to expectation.
Willie Jacobs
7/24/20234 min read
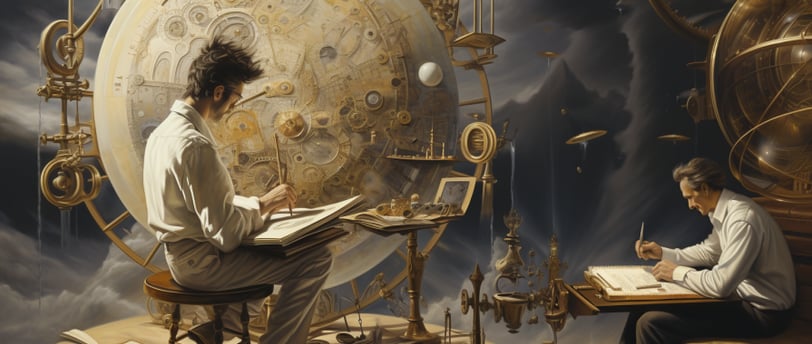
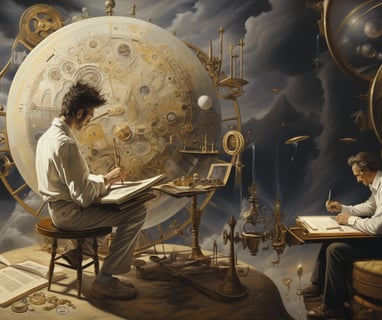
If you have been in the mining maintenance game for a while, you know that the phrase "maintenance planning" can conjure up many emotions... and it sure covers the spectrum - from "what planning?" and the frustration of trying to get something useful out of a super powerful (or so they promised) ERP (or CMMS) system that was poorly configured, to the joys of being able to see the future play out with some confidence.
If I may ask... where are you (personally) on this spectrum?
Planning basics
As we continue to work with clients, we keep seeing this spectrum filled. As much as I do not like to go back to the cliched "back to basics", it seems ever true. Here are some foundational planning elements to consider:
Asset register - you cannot have a maintenance strategy for something that is not on your asset register (and... no - the fact that Bob / Sue never forgets is not a suitable plan). That includes the machine that was "just brought on for a 1 month job". You know - the really useful one that has never left site for the last 2 years? Or those main support beams from which your towering plant structure hangs...
Criticality - Every asset is not equal in terms of overall value for the business. Trade-offs will have to be made (and priorities set), so understanding which assets come first in line is important (you can choose where the boss' vehicle lies in this hierarchy :-)
Maintainable elements - at what level do you pitch your maintenance activities? There is no one-size-fits-all, but "Truck 21" is too high a level and "bolt 16 on the left final drive" is too low a level.
Threats - what does failure look like for each maintainable element? "That sounds like a lot of work to map that for every maintainable element" you may think, but guess what - without understanding failure, you cannot choose the best maintenance strategy
Strategy options - ...and yes... there are options! In some cases, fix when fail is actually a valid option. Once you have a clear view on criticality, you can consider cost of each strategy and cost (impact) of downtime - taking both into account can steer you in the right direction.
Strategy selection - once you understand which is the best strategy, work can then begin on developing the task list, materials and resources required. Technical input is vital here (and that includes suppliers / dealers but is not exclusively theirs to do).
Once you have worked through this, you are ready to have something to feed into that powerful ERP (or CMMS).
Some common mistakes
Leaving it for later: During the mine project / setup phase, the temptation is to leave the planning setup for the operational team to do. Setting up the planning infrastructure and system is a vital part for the Operational Readiness team. When the pre-stripping starts during the warranty period... the system needs to be fully set-up and operational.
Left for the OEM dealer: "Surely they have this stuff" is a phrase I often hear from mobile equipment maintenance teams. The reality is that dealers do not often do maintenance planning (the era of outsourced dealer-maintenance is fading) and, although they can add much value, dealers very seldom drive the process. Each client site is different (severity, application, environmental conditions) and standard maintenance interventions require site specific inputs and alterations.
Multiple versions of "the truth": I read an article a couple of weeks ago that stated that >90% of businesses still use MS Excel as a foundational tool in running their businesses. How much of your planning is done in Excel vs. in your ERP system? I understand that using Excel (or PowerBI) for reporting is a great option, but if you have an ERP / CMMS and you are still doing large parts of your planning in Excel, there is work to be done. Excel's greatest advantage (the fact that you can "fiddle" with the numbers) is also its greatest weakness, especially in sites where you have rotations.
Inconsistency of process: "How often do you hear "I'm not sure how they do it here, but at my last place..." - combine that with a rotation roster where cross-shifts do things in their own way, and you have a recipe for frustration and inefficiency.
These basics have not changed, and no matter how powerful an ERP you have in place, without these basics being properly configured, much of the power of that (expensive) ERP will remain untapped.
Wrapping up
The complexities of maintenance planning in the mining industry cannot be overstated. It's a critical process that, when done right, can significantly improve operational efficiency, reduce downtime, and ultimately, boost the bottom line. However, it requires a thoughtful approach, a solid understanding of the unique challenges each site presents, and a commitment to getting the basics right.
Whether you're just starting out or you're grappling with a system that's been poorly configured, remember that it's never too late to reassess and make improvements. The power of a well-configured ERP or CMMS system is immense, but only if it's built on a solid foundation of planning basics.
Your thoughts
I'd love to hear your thoughts on this topic. Have you faced similar challenges in your maintenance planning? What strategies have you found effective? Please share your experiences in the comments below.
If you're currently facing challenges with your maintenance planning and could use some expert guidance, don't hesitate to reach out. With over 20 years of experience in the mining industry, we can share some thoughts and help you navigate these complexities.
Get in touch
We would like to connect and know how we can support you and your team.